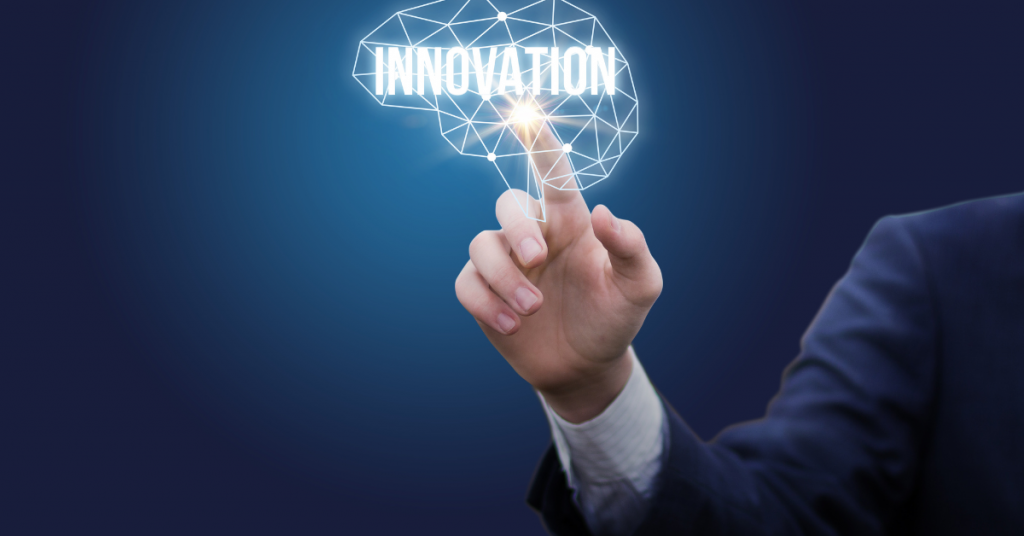
Plastic plays a key part in everyday life, from storing drinking water to protecting food during transport. As demand grows across the continent, manufacturers must balance cost, quality and environmental impact. By using modern technologies and responsible practices, suppliers can deliver plastic solutions that meet local needs while reducing waste and energy use.
Modern Manufacturing Meets Sustainability
Today’s plastic makers use advanced machines that shape raw resin into durable containers and parts. Injection moulding presses allow precise control over material flow, cutting down on excess scrap. Stretch blow moulding uses carefully heated preforms to produce uniform bottles for water and soft drinks. These methods use less energy than older processes and generate fewer offcuts. An efficient plant reuses its own trimmed pieces, melting them back into the production cycle. This lowers the need for fresh resin and cuts the overall carbon footprint.
Reducing Waste Across the Supply Chain
Waste reduction starts before a single item is made. Engineers design moulds so that every gram of material counts, and adjust wall thickness to retain strength without overuse. Automated systems measure weights in real time to flag any out-of-tolerance batches. When production lines halt for maintenance, teams collect and sort any remaining resin so it can be reprocessed. By linking quality control to traceability software, managers know exactly where every kilogram of plastic goes, helping to meet strict environmental guidelines.
High-Quality Products for Diverse Industries
From food and beverage to chemicals and cosmetics, many sectors rely on reliable plastic components. Containers for household cleaning liquids need to resist chemical attack, while medical packaging must meet hygiene standards. Manufacturers supply water bottles for water dispenser and robust water dispenser bottles, as well as sturdy water cooler bottles for office and home use. Computer-aided design models stress points before a mould is cut, ensuring new water dispenser bottle caps seal correctly and that large drums stack safely in warehouses. Clients benefit from faster turnaround on samples and stable performance once full production begins.
Innovation Through Research and Development
Staying at the forefront of plastic technology means continuous investment in research. Material scientists test new resin blends and work closely with a leading PET bottle manufacturer to improve impact resistance or lower melt temperatures. Process engineers refine screw designs and cooling channels to speed cycle times. Pilot lines trial PET preforms and recycled content before rolling successful mixtures into full-scale runs. This approach gives clients access to greener options without sacrificing performance.
Local Impact and Community Benefits
Producing plastic goods close to end users cuts transport costs and reduces delivery emissions. When factories operate in towns outside major cities, they create skilled roles in machine operation, maintenance and quality assurance. Local suppliers of electricity, water treatment and waste management also see economic gains. By training staff in efficient plant practices, companies boost safety and consistency. Over time, this builds confidence among clients seeking reliable supply chains in Africa.
Embracing Circular-Economy Principles
A truly sustainable approach treats plastic not as throwaway material but as a resource to keep in use. Return-and-refill schemes for large water containers help extend product life. Collection networks send empty drums back to cleaning and refilling stations rather than landfills. Some producers support community collection points for used packaging, feeding clean scrap back into production. These efforts lighten the load on municipal systems and offer buyers a clear route to reduce their own environmental impact.
Meeting Regulatory and Quality Standards
African markets follow a growing body of regulations on food contact, chemical leaching and import specifications. Adopting international standards such as ISO 9001 for quality management or ISO 14001 for environmental systems helps maintain consistency across batches. In-house laboratories check for contaminants, colour fastness and dimensional accuracy. This diligence ensures every delivery meets client expectations and keeps operations running smoothly, even as regulations tighten.
Partnering for Tailored Solutions
Every customer faces different challenges. A beverage brand might need a lightweight water cooler water bottles design, while a chemical supplier requires heavy-duty drums with tamper-proof lids. Strong partnerships start with careful needs analysis and rapid prototyping. Engineers work alongside clients to refine designs and test functionality. By using digital feedback loops and regular site visits, manufacturers adapt quickly to changing demand, whether it’s a surge in orders or a new sector requirement.
Building a Greener Future in Africa
As Africa grows, so does the need for reliable, sustainable plastic products. By combining high-tech production lines with waste-cutting practices—from sourcing lightweight resins to ensuring secure water bottle caps—modern plants deliver sturdy, consistent items at competitive rates. Communities benefit through job creation and reduced environmental strain, while clients gain peace of mind that their packaging meets global standards. When plastic is made and managed responsibly, it becomes part of a healthier, more productive economy rather than a disposability problem.