Metal fragments in a production line can damage machines, contaminate products, and cause unplanned downtime. Adding detection devices to conveyor lines helps catch unwanted metal before it reaches critical equipment or finished goods. This article explains how these systems work, what types are available, and how to keep them in good condition. You will learn simple steps to pick and care for the right unit for your needs.
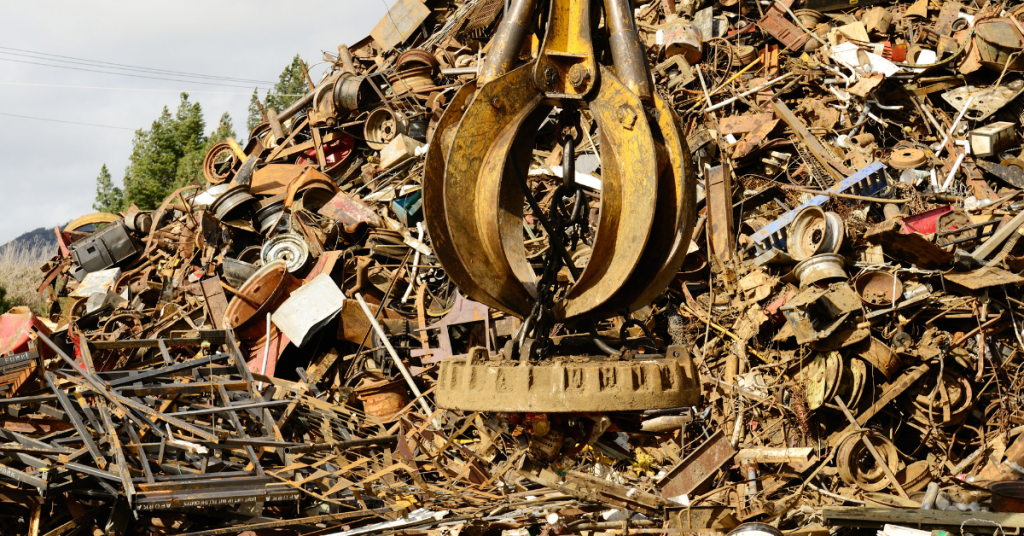
How Metal Detection on Conveyors Works
A metal detection unit uses an electromagnetic field to sense metal as material moves on a belt. When metal passes through the field, it disturbs the balance and triggers a signal. The system then kicks in a response, such as stopping the belt or diverting the flow. This quick action keeps sharp pieces from reaching sensitive parts or ending up in boxed products.
Conveyor Metal Detector Options
There are several styles to fit different lines and budgets. A conveyor metal detector sits above or below a belt segment. It checks everything on the belt without touching the load. For a more complete setup, a metal detector conveyor system bundles the detector with automatic belt stops and a reject gate. This saves floor space and makes installation simple.
In tight spaces, a metal detector in conveyor belt model fits inside the belt frame. It uses a slim coil that slides under the belt surface. This design limits height impact and works well where headroom is low. An alternative is the belt metal detector, which mounts on the belt’s side and senses metal through the moving belt edge.
Industrial Strength Units
Heavy duty lines that handle rough or wet products need a tough detector. An industrial metal detector conveyor unit is built with stainless steel housing and sealed controls to stop dust and moisture from causing faults. These units run in food, mining, and recycling plants without extra covers. They resist corrosion and keep working even when washdowns occur.
Adding Separation and Cleaning
Some lines combine metal detection with a catch system. A conveyor belt separator adds a reject chute or arm that pushes metal pieces off the belt into a bin. This reduces operator work and speeds up the removal process. A similar setup called a conveyor separator uses air blasts to blow contaminants aside. Both methods work without shutting down the belt.
Keeping belts free of dust and residue is also key. A conveyor belt cleaning unit uses blades or brushes to wipe the belt as it returns. This stops build up that could hide metal or wear down detector coils. Clean belts help the system spot small fragments more clearly and lower false alarms.
Testing and Calibration
To keep a detection line sharp, run regular checks with a test piece. Gauss testing tools measure the field strength and show if the coil has lost power. If readings fall below the maker’s specs, the unit may miss small fragments. A quick magnet testing step with a calibration block ensures the detector still reacts as expected. Make records of each test and adjust sensitivity if needed. This simple practice keeps product safety high.
Installation Tips
When fitting a unit, place it after any magnetic or metal removal step. This way it catches stray pieces that slipped past. Allow enough flat belt run on each side so the product settles before detection. If space is tight, choose a slimline detector that fits inside a standard frame. Mount controls at eye level for easy reach. Run wiring in conduit or cable trays to guard against damage.
Maintenance and Troubleshooting
Daily clean the sensor faces and wipe off any dust or grease. Check belts for tears or uneven wear that could affect detection. Inspect cables and connections for signs of wear or loose plugs. If you see frequent false trips, run a test piece and adjust the threshold to match your product profile. For units with reject gates, confirm the gate fires and returns smoothly. Schedule in-depth checks monthly to cover all points and log findings.
Real-World Example
A snack food plant added a Conveyor metal detector right before baggers. They ran small steel pins through each line in the morning test. The detector trapped two pins that had mixed in during cleaning. Without the unit, pins would have hit packing machines and stopped lines for repair. After adding a simple belt scraper, team members saw fewer false alarms and needed less time fixing jams.
Picking the Right System
To choose the best setup, start with your product type and speed. Dry, free-flowing items work well with overhead detectors. Wet or sticky items pair better with flush-mounted coils. Match the unit’s belt width to your line and note the frame height. Ask about service options and local support since quick repairs cut downtime. Finally, compare features like auto-set sensitivity and remote alarm outputs to suit your site needs.
Using metal detection on conveyors brings peace of mind and keeps your line moving. With clear steps for testing and cleaning, teams can stay focused on output instead of surprise breakdowns. Adding the right detector and following a simple care plan helps protect equipment, boost safety, and maintain product quality.